SkyCiv and its modules are a powerful set of tools from which users can model, analyze, and design. Due to its intuitive and powerful 3D modeling and analytical capabilities, SkyCiv 3D allows for multitudes of variability for structural engineering projects. In the case of Mitch Frumkin, President of Kipcon Engineering, this is experiences first hand for a variety of remediation and rehab projects. Today we will explore the challenges of such a project.
Apex Power Project, Las Vegas, NV. Type: Industrial Engineer: Kipcon Engineering
Kipcon Engineering is a full-service engineering firm founded by Mitch in 1983, and offers a wide structural expertise. A unique project line of theirs is the remediation of air cool condenser support structures.
To complete the project, Mitch reflects "I was looking for a program that needed comprehensive 3D capabilities. I use it extensively, and I love it."
About the Project
Located 35 miles outside of Las Vegas, Nevada, the original structure stretched roughly 200 x 240 feet and stood 117 feet tall. The heat exchangers of the air cool condenser and the 34 foot diameter fans are supported by a steel frame, with the columns being designed for axial load only. In the original design, wind is not factored in the steel design because the wind would flow right by the steel members, given it was an open structure. However a redesign was required as the wind was flowing by too fast and not being captured by the air cool condenser, resulting in huge inefficiencies for the client since the unit was being under-utilised. Mitch presented this project and its challenges at the Combined Cycle Conference 2019 in St Louis.
The Challenge
For the remediation, Mitch was tasked with re-evaluating all of the original members and coming up with a cost effective solution to increase the efficiency of the air cool condenser.
Mitch looked to the technology of Galebreaker Industrial for a solution. Galebreaker Industrial invented a patented Wind Screen consisting of a woven polyester fabric with a PVC coating that captures the wind and supplies the units with a steady air flow. This would however create a set of challenges in that the structure was never designed to take such wind loads. Mitch would have to reinforce the structure after installation of wind screens all around the exterior of the frame. When wind flows toward the screen, the two adjacent columns feel that lateral load as well as the tensile force from the cables pulling in from the deflection of the screen.
These two new loads put some of the retrofit columns into biaxial bending, something that Mitch was able to analyze and design for using SkyCiv 3D, when he couldn’t find the capability elsewhere. “I was looking for a program that needed comprehensive 3D capabilities,” Mitch reflects, “now I use it extensively and I love it!”
This unique loading scenario was a breeze for Mitch to model and look at the live results. He was able to quickly identify and single out columns, beams and bracing that needed to be retroactively supported.
How it was Designed
Mitch started off by modelling the entire structure, with the load of the air cool condenser. During the modeling of the original structure, Mitch took advantage of some easy-modelling functionality such as repeating; creating a single frame line and duplicating it over the number of bays in the structure. He found that the color differentiation of the members shown in the wireframe version of the 3D space to be clear and concise. Once the model was constructed, Mitch took full advantage of the hide tool to have a closer look at a single frame line to verify and ensure accuracy between the analytical SkyCiv 3D model and to include in his reports.
Once the problem areas were identified, Mitch used the seamless integration between the SkyCiv 3D module and the SkyCiv Member Design Module to aid in his final design efforts. An unsung feature that was prominent in his deliverables to the client were the thorough and in-depth member design reports generated through the SkyCiv Member Design module.
How SkyCiv Helped
When asked how SkyCiv helped, Mitch responded with a series of benefits around SkyCiv’s customer service and the technical capabilities of the software.
Fast and Professional Customer Support
His number one comment was that: “SkyCiv’s customer service is spectacular. I typically get a response in a matter of hours via live chat, and not have to wait around for more than 24hrs like with other software”.
This support helped Mitch get through his project faster, with fast and effective responses to his software-related questions and assistance in troubleshooting helped him turn the designs around faster. “I think at one point I needed the Chinese Steel members, which weren’t in the catalogue. I emailed support and they added it into the software the same day!”
Clear and Open Reporting
As for technical benefits, Mitch found the open calculation reporting extremely useful. With SkyCiv’s clear and open reporting, with referencing to AISC. Help me follow what the software is doing. “These things are awesome - it’s like somebody did it by hand.” When combined with the filtering functionality, this helped Mitch identify the failing members and “use the report to determine where or why it was failing which enabled me to changed the bracing to get it to pass.”
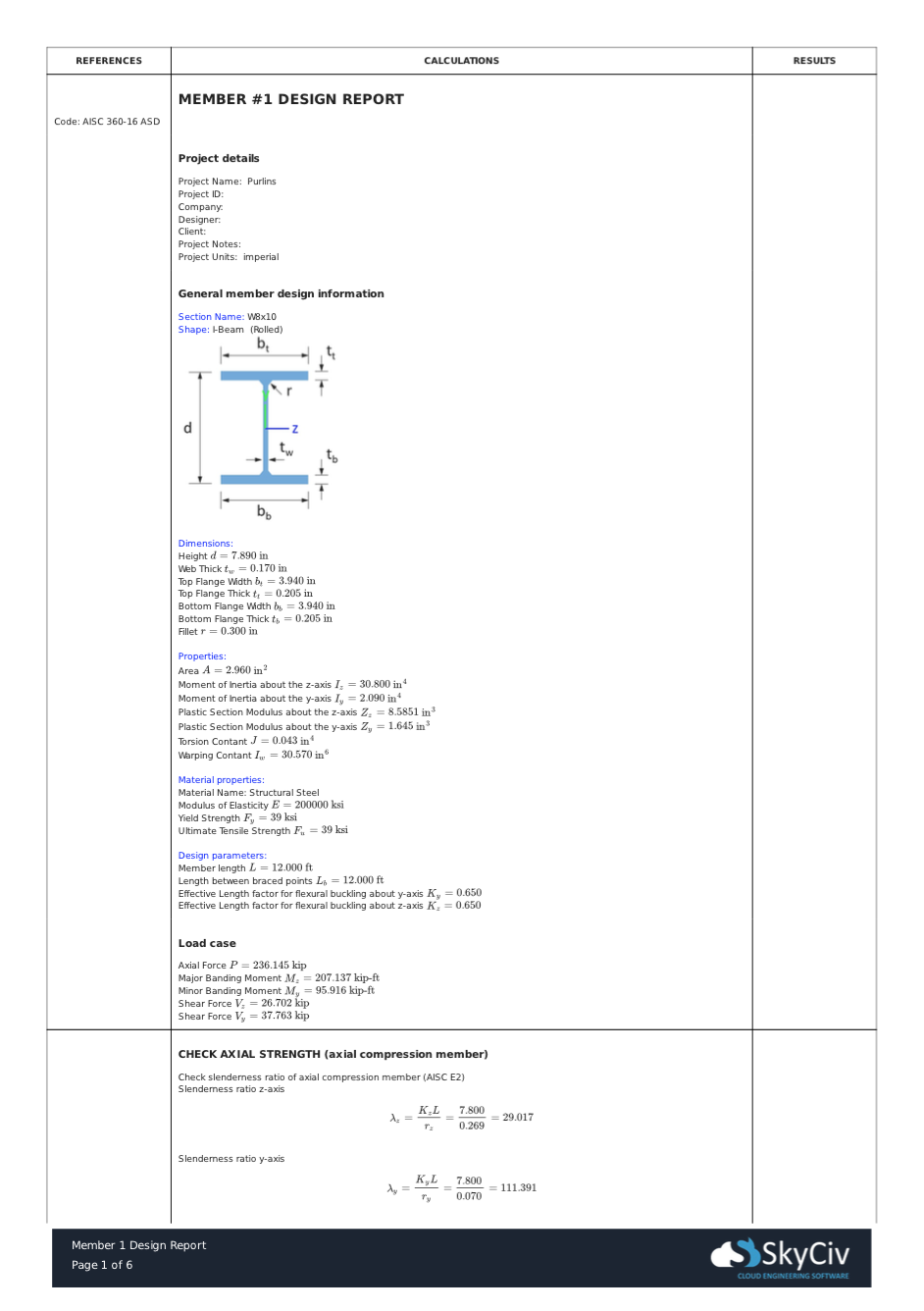
Haven't tried SkyCiv yet? Get started for free today!
CEO and Co-Founder of SkyCiv
BEng (Civil), BCom